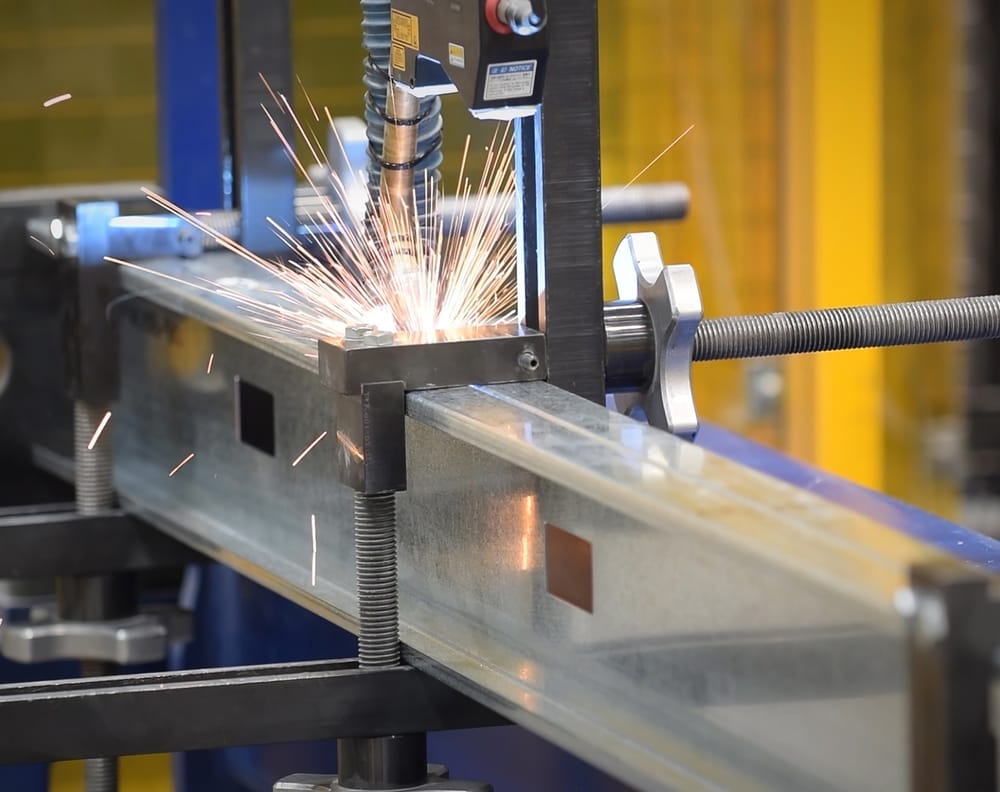
The digital prefabrication advantage
Prefabrication delivers quality, cost savings and speed on all types of projects.
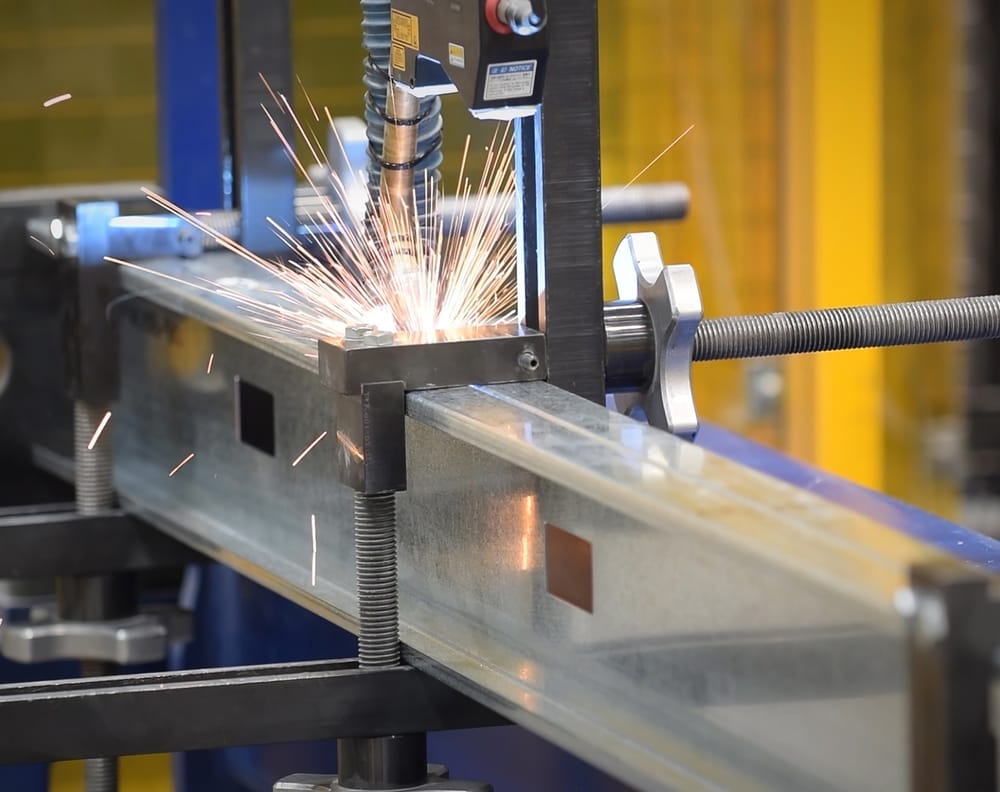
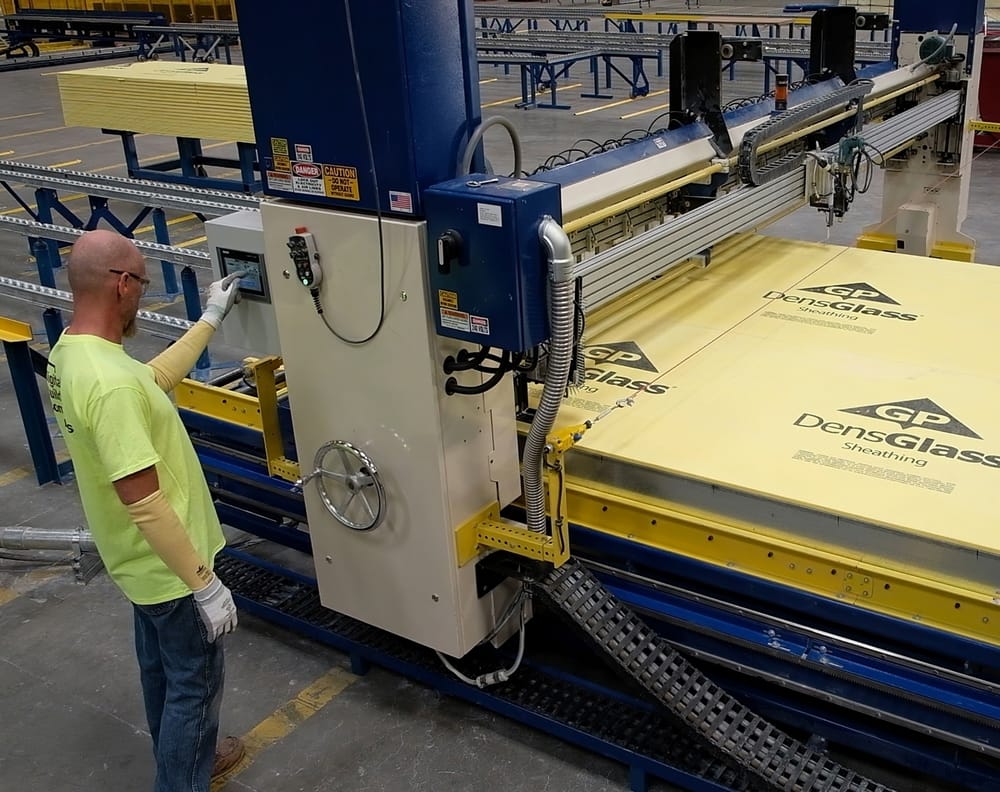
A version of this article was originally published on dpr.com in March 2020.
The construction industry is developing new methods and improving productivity in response to customer needs, technological advances and labor-related challenges. Digital fabrication–a type of prefabrication where digital data directly drives manufacturing equipment to form various building components – is at the forefront of this evolution.
Today, componentized building elements have been proven to deliver high-quality projects with lower costs and accelerated schedules. Concepts like DfMA – design for manufacture and assembly – and DIMC – designing for industrialized methods of construction –are on the rise. Both support concurrent engineering methodology, as well as an industry shift from field construction to field assembly.
According to Buildoffsite, DfMA, in its simplest terms, is “the application of factory (or factory like) conditions to construction projects” and almost always includes prefabricated components. Parts of the structure are manufactured offsite in a controlled environment. These pieces are then delivered to the job site and hoisted into place for assembly.
DIMC, on the other hand, evaluates how available building components can be programmatically arranged and procured in the most efficient ways to provide cost and schedule certainty, along with improved design and construction quality.
Custom Solutions, Powered by the Virtual Model
But what about creativity? Does building with prefabricated components restrict customization in design? It doesn’t have to.
Digital Building Components digitally fabricates precise-to-spec building assemblies directly from the building information model (BIM), including load-bearing panelized structures, fully finished panelized exterior walls and panelized interior walls with electrical and plumbing already roughed in.
The key to integrating digital fabrication is to include it from the beginning of the design process. Digital Building Components collaborates with customers, general contractors, architects and engineers to determine if prefabrication makes sense and how best to include it.
Each project is a blank canvas. Custom structures are built to fit the unique needs of each project by leveraging virtual design and construction (VDC) processes and the data-rich building model. Digital Building Components works with each project team to identify the best options for maximizing the architectural design for the DfMA process, without changing the design. This helps ensure that the project will run smoothly, and avoids the challenges arising from inserting prefab into an existing design.
Work in Action
Digital Building Components worked with DPR, a national general contractor, on the 175,000-sq.-ft. Building 1 on the Vantage McLaren Santa Clara data center site to deliver our first use of pre-finished EIFS panels. The digitally fabricated exterior panels allowed the team to enclose the building nearly 12 weeks earlier than if it had been stick-built.
In a series of higher education projects in California, Digital Building Components also provided prefabricated steel panels in place of wood framing, without increasing the owner’s cost. According to the owner, the projects realized the following benefits by including prefab:
- Efficiency of construction
- Improved schedule
- A stronger, better product for the same cost.
Ultimately, the power of digital fabrication is in the value to the customer and project. Digital prefabrication employs advanced technology to improve quality, lower costs and speed up the schedule, while leveling out the labor. Improved modeling capabilities that streamline the connection between design and construction place prefabrication at the forefront of the technology revolution that is transforming construction.
Key Benefits
Incorporating digital fabrication into a project’s design can yield the following advantages:
- Higher Quality: Digitally fabricating components in a factory-controlled environment improves quality control. Machines create precision products directly from the model and deliver components that fit as expected in the field.
- Cost Certainty: Materials are batched, and waste is reduced or eliminated. Factory-based labor offers greater predictability that results in higher productivity, safer working environments and cost advantages. According to Buildoffsite, site labor costs about 2.2 times as much as factory labor and factory productivity is about double that on jobsites.
- Accelerated Schedules: Panels are manufactured in parallel with work done in the field. This leads to earlier project completion. Weather doesn’t affect factory production and thus becomes less of a factor.
- Improved Labor Resources: A 2019 survey by AGC found that “80% of contractors report difficulty finding qualified craft workers.” Prefab requires fewer workers, provides a safer work environment, and offers consistency - making jobs in the prefab sector among the most attractive in the construction labor force. Controlled environments also allow for cross-training in specific tasks, which helps in labor balancing, skills enhancement and workforce improvement across the board.
- Sustainability: According to the World Economic Forum (WEF), “About 40% of solid waste in the United States derives from construction and demolition.” Prefab batches production and takes place in a controlled environment, substantially reducing or eliminating waste. It also reduces the number of vehicles traveling to and from the jobsite, thereby reducing the consumption of fossil fuels and their associated emissions.
- Other Job-specific Advantages: Jobsite constraints are becoming more common. Prefabrication minimizes the number of workers required on-site. According to Sam Huckaby of Vantage, having fewer people on the jobsite was a significant benefit of using prefab. “We were a constrained site from a parking and access perspective, so the more work we were able to do offsite, the better, especially when something is wrapping the entire building…”